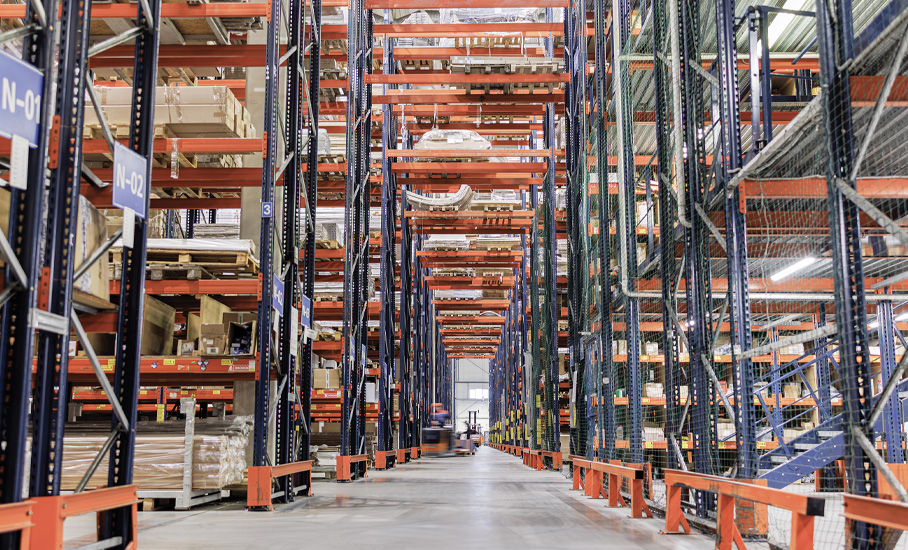
In early 2021, NRCA issued its first update to members about irregularity in the availability of some roofing materials. At the time, the issue was relatively minimal: There were some worrying indications of a supply and demand imbalance.
The industry had been through other shortages following severe weather events that spiked demand, decreased supply or both. Those shortages were temporary and something the industry could plan around. But in 2021 amid the COVID-19 pandemic, the entire industry was not prepared for the material shortages that would last well over a year.
I won’t go through the chronology in detail because we all lived it once already. But having put a few years behind us to let the wounds heal and “normalcy” return, it seems worth revisiting as a testament to our industry’s tenacity and to reflect on where we are now and where we may be heading.
First, manufacturers were hit with raw material procurement issues early and throughout the supply chain. Port backups, shipping and logistics meltdowns and weather literally freezing factories to a halt all affected manufacturers’ abilities to make their products. Many went to great lengths to keep their lines running. One manufacturer representative recently told me his company was putting pallets of raw materials onto cargo planes and flying them across the ocean to keep things running.
Second, people in the U.S. bought all the toilet paper and contractors bought all the roofing materials along with it. Panic buying, strategic buying, hoarding, call it what you will: It happened. Well into my first year as NRCA CEO in late 2022/early 2023, I was visiting contractors and would hear different versions of the same story: “This is where we used to keep the [fill in the blank], but it’s where we keep the ISO now.”
Meanwhile, when hearing about the “material shortages” contractors were saying they were experiencing, manufacturers would say: “We are making more product than we ever have. There is not a material shortage. It’s a demand issue. Ghost orders are sucking everything up. There wasn’t enough labor to install a small amount of squares six months ago. How are 30% more squares being installed now!?”
Add a few expletives in there to personalize it, and that gist was repeated to me more than once. Often loudly.
But like a traffic jam that grinds cars to a halt only to clear 1 mile later with no sign of the source of the backup, that was the roofing industry. Everyone behaved rationally for themselves, but it put the collective industry in worse shape.
Although no amount of logistical improvements and supply growth can fully defend against a massive spike in demand, the industry’s supply chain is more resilient and less risky than it was in 2022
In the years since, many manufacturers have bolstered and diversified their supply chains to make them more secure and stable. They have looked at the supply chain through a geographic lens and worked on onshoring or nearshoring their materials and production. Rather than buying a critical component from China, for example, some have developed sources in the western hemisphere and increased their domestic production. They recognized the fragility of their logistics and have taken steps to improve them.
Trucking, cargo ships and freight rail were all stretched beyond capacity in 2022, and companies are more aware than ever about logistics weak points. Many have downshifted from the “just in time” inventory gospel of past decades to maintaining buffer inventory to allow for any shipping slowdowns that can easily arise. This has proved helpful as we have recently experienced port strikes, threats of strikes, pirates and weather events.
Manufacturers not only have brought raw materials closer to the U.S. and improved their logistics situations, but they also expanded capacity. Since 2022, three new polyisocyanurate plants have opened in the U.S., and a fourth has been overhauled to increase output. And additional plants for insulation and membrane production are in the design and discussion phase. New fastener production machines have become available, and shingle production capability continues to rise.
I’m writing this column well before Donald Trump’s presidential inauguration, and we don’t know for sure what tariffs may be put in place, but the early discussion and statements coming from Trump’s transition team is something manufacturers and the industry are watching closely.
Several raw materials our industry relies on already have large tariffs on them, so preliminary indications are prices may rise some but will not be overwhelming. The example given to me about a specific item produced in Asia was: “The tariff is currently at 800%; raising it to 810% is negligible.”
What happens with oil from Canada, cement from Mexico and hundreds of products across the spectrum of our industry will remain to be seen.
An additional unforeseen aspect of our supply future is how nations respond to any U.S. trade actions. China and Mexico have indicated they intend to respond in-kind to any actions from the U.S.
For example, China announced a ban on sales to the U.S. of antimony, a mineral used in many fire retardants. China put this ban in place in response to the U.S. restricting computer chips going to China. We should expect this type of volleying will continue and perhaps accelerate, and manufacturers will have to remain flexible and highly responsive to the changing dynamics.
If a membrane manufacturer can no longer get antimony to include in its formula and maintain its fire rating, what does it do? Chemists and engineers have alternatives and solutions at the ready.
Although no amount of logistical improvements and supply growth can fully defend against a massive spike in demand, the industry’s supply chain is more resilient and less risky than it was in 2022. The effects of trade fights among nations remains to be seen, but the industry is paying close attention and proactively preserving supply lines and remaining competitive with pricing.
There is no guarantee all the toilet paper (or screws) in the nation won’t disappear in the months ahead, but it is less likely than it was a few years ago. It seems prudent for contractors to not revert entirely to the long-standing practice of last-minute orders. If it is essential a roof component be on-site at a specific time and day, be sure to allow extra time for life’s curveballs. They are likely to continue.
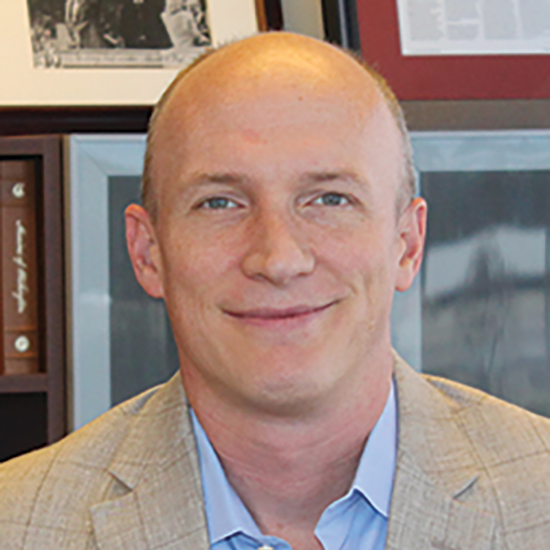
McKay Daniels
CEO
NRCA