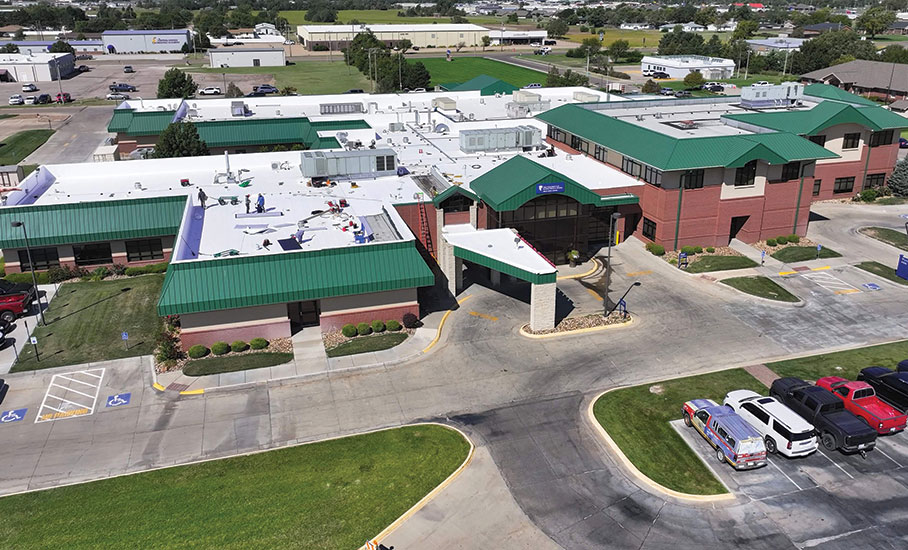
The University of Kansas Health System is a nonprofit, academic medical center in Kansas City with three branch hospitals and educational centers throughout the state. It is the region’s only nationally verified Level I Trauma Center. In 1998, it became an independent entity that receives no funding from the state. It is affiliated with the University of Kansas Medical Center, Kansas City, and its physicians represent more than 200 specialties.
The Great Bend campus serves communities surrounding Barton County. In July 2023, a hailstorm damaged the facility’s roof, causing damage and water leaks. Rhoden Roofing LLC, Wichita, Kan., was selected as the roofing contractor for the project.
Repairs first
Before the storm, the polymer-modified bitumen roof membrane on the University of Kansas Health System Great Bend Campus facility showed signs of aging but remained in good condition. The membrane was beginning to deteriorate, including granule loss, but it still had useful life left. Leaks were minor and confined to areas around HVAC units.
But the severe hailstorm that produced hailstones between 1 1/4 and 1 1/2 inches in diameter accelerated the roof system’s decline. Granule loss on the membrane increased, and the parapet walls took the brunt of the damage as 70 mph horizontal winds drove hail into them. Of particular concern were holes in unsupported areas where the walls transition to the roof field.
The team at Rhoden Roofing immediately made repairs to make the roof watertight and keep the hospital functioning without disruption. This included temporary patchwork on the parapet walls.
New roof planning
The hospital roof remained structurally sound and was an ideal candidate for re-covering. To verify this was the best option, the Rhoden Roofing team made core cuts in areas of concern. There were a few areas where the insulation was saturated and the roof deck damaged, requiring replacement, but a complete tear-off and replacement was not necessary. Maintaining hospital operations while installing a new roof was a top priority.
“Re-covering the existing roof would be faster and cost far less than a full tear-off,” says Brett Worrell, project manager for Rhoden Roofing. “The building’s interior would not be left exposed to the elements, and disruption to the hospital’s daily activities would be minimized.”
The University of Kansas Health System was a new tenant in the building owned by Cleveland GB Investors LLC, Wichita, Kan. It was important for the building owners to install a new roof that would provide reliable, hassle-free service for the duration of the long-term lease.
It also was essential to protect everyone and everything inside the hospital while the work was being done on the roof. The hospital could not shut down and had to continue serving the community and seamlessly caring for patients.
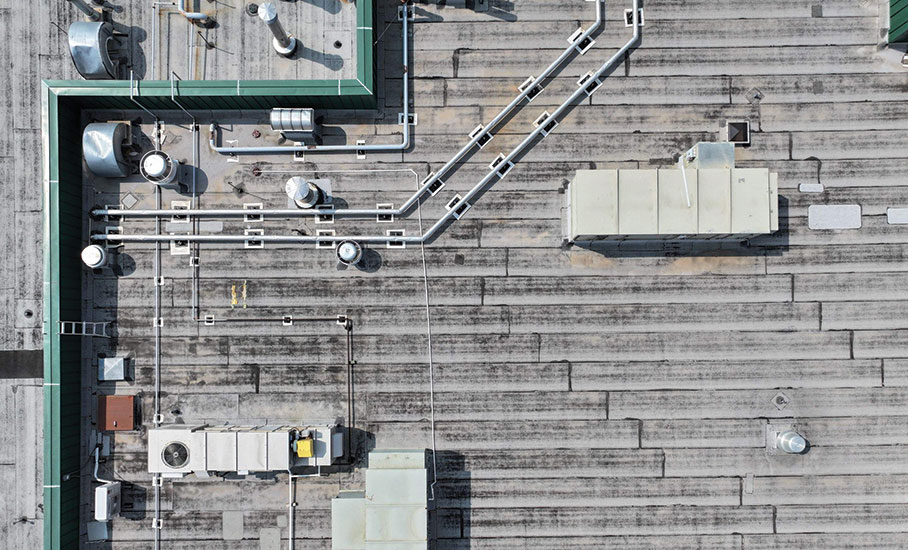
“There is a lot going on in the hospital, and it has a lot of expensive equipment,” Worrell says. “Re-covering the roof limited everybody’s risk while also giving the client a roof that would be useful for another 20 to 30 years.”
The Rhoden Roofing team recommended new white TPO membrane for the Great Bend facility’s roof.
“It was the best option,” Worrell says. “We like TPO and how the seams come together and are heat-welded. It is stronger in the seams than EPDM. We prefer fleece-back TPO membrane that can be adhered directly to many existing roofs.
“Also, the average high temperatures from June through September in Wichita are in the mid-80s F to low-90s F. The white membrane will help the hospital reduce its cooling costs and maximize the efficiency of the building’s HVAC equipment while keeping patients, staff and visitors comfortable.”
To secure the new roof contract, Rhoden Roofing had to gain the confidence of the building owners and the hospital’s board of directors. Communication and responsiveness were key.
For example, during Worrell’s first meeting with the hospital’s board of directors, the hospital’s head of maintenance called in to the meeting to inquire about the cost to replace a coping cap. Before the end of the meeting, Worrell was able to determine and provide the cost. A few days later, Rhoden Roofing was awarded the contract to re-cover the roof.
“If a client needs information, it’s crucial to get it to them right away,” Worrell says. “In this case, the board members knew if they asked questions, they would get answers. And things would get done.”
“Brett created trust with the building owner and tenant by making sure they knew the system put on the roof would be the correct one,” adds John Rhoden, owner of Rhoden Roofing. “He assessed the roof and explained they could save some dollars with a roof re-cover versus ripping out the entire roof.
“The board had confidence it would get a high-performing roof and Brett wasn’t throwing things in just to increase the bill,” Rhoden continues. “Brett’s ability to be responsive to their questions by researching and providing the right answers was critical to our being able to earn this project.”
Installation
It took more than a year for the final plan to be approved, funding to be secured and work to begin. In August 2024, the Rhoden Roofing team began the installation phase. Workers swept and cleaned the 51,600-square-foot roof surface to prepare for the new TPO membrane.

The existing polymer-modified bitumen roof membrane had been installed in two phases during 2001 and 2008. Phase one work included polyisocyanurate insulation on the metal roof deck. Some areas applied during phase one contained membrane blisters. Team members cut out these areas so the new TPO membrane would lie flat properly.
The crew used MuleHide Helix® Max Low-Rise Adhesive in the roof field to adhere MuleHide Fleece Back TPO 60-mil membrane directly to the existing roof membrane.
“Because we used a fleece-back membrane, there was no need to add a cover board as a separation layer,” Worrell explains. “That sped up installation and reduced labor and materials costs.”
On the 6- to 8-foot wood parapet walls, the crew used MuleHide AeroWeb Low-VOC Aerosol Contact Adhesive/ Primer to adhere standard TPO 60-mil membrane.
“Given the hospital’s layout and the parapet walls, overspray was not a concern, and spray application was much faster than using a roller,” Worrell says.
Safety
A significant safety concern was working around the numerous rooftop HVAC units and the natural gas lines that power them.
“The rolls of fleece-back TPO are large and heavy, and accidentally bumping one of them into a gas line could easily have caused a potentially catastrophic gas leak,” Worrell says. “The need to take extra care when working around the gas lines—and the location of the main shutoff and how to use it in the event of an emergency—were major points of emphasis during crew meetings.”
When moving materials from the on-site staging area to the rooftop, crew members on the ground directed vehicular traffic and ensured the crane or telehandler was positioned securely in place so vehicles could navigate safely around the equipment.
Crew safety also was top priority. The team followed all Occupational and Safety Health Administration safety regulations and company practices.
“Everybody walked away safely,” Worrell says. “Everybody went home every night. That is always important.”
Helipad
The University of Kansas Health System Great Bend Campus has a helipad to receive and transport critical patients at its trauma center. Although the helipad itself is adjacent to the roof, the related communication equipment, windsocks, lighting and warning systems are on the roof.
Accordingly, on days when Rhoden Roofing had to use a crane or other heavy equipment on-site, the team communicated with hospital staff so the helicopter pilot would be alerted of a potential hazard. When necessary, roofing work was paused and/or the equipment relocated.
“We communicated proactively so the customer always knew where and when there was a crane on-site,” Worrell says. “We explained how we were going to approach work every day and every week and what we would be doing the following week.”
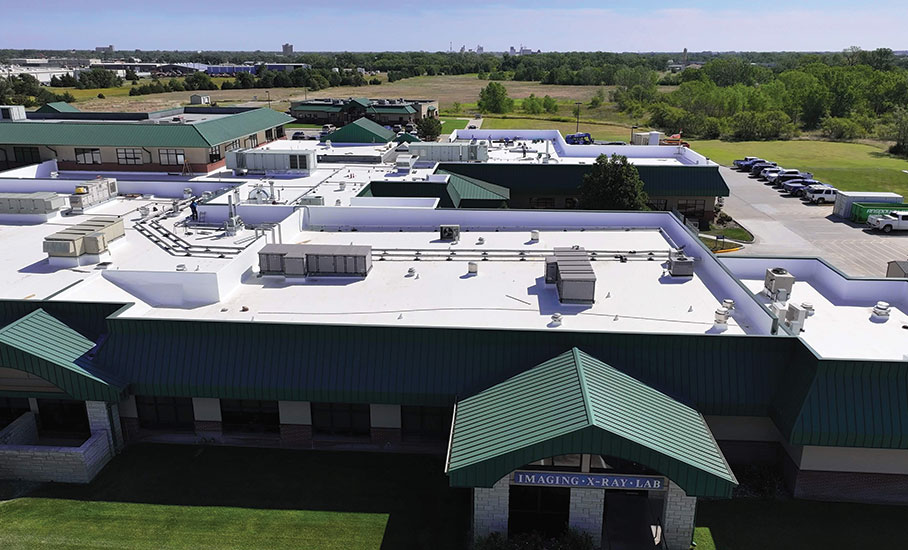
When the helipad’s communication equipment needed to be disassembled to install the TPO membrane, Rhoden Roofing team members coordinated with the hospital’s electrician to ensure the equipment was brought back online quickly to resume helicopter flights. The process was completed in two hours.
“We knew it was important to the hospital, so it was important to us,” Worrell says.
Ongoing communication among the roofing crew and hospital staff was essential to ensure the project proceeded smoothly.
“You can plan and prepare, but if you don’t communicate, you may as well not plan and prepare,” Worrell says. “You can’t just slap on a roof. The planning, preparation and communication that took place on this project made it so the customer hardly knew we were there, and we only had to close a small 12-space parking lot for equipment.”
“Brett had a really good understanding of the business operating within the building,” Rhoden says. “A lot of contractors can talk roof systems, but Brett recognized when you’re working on a hospital, not interrupting its operations is the number one factor.”
Fully recovered
On Sept. 25, 2024, the Rhoden Roofing team wrapped up work on the University of Kansas Health System Great Bend Campus facility, five days ahead of the timeline.
Thanks to diligent research and persistent and thorough communication exercised throughout the project’s duration, the roof re-cover project met the needs of the building owner and hospital staff and was an overwhelming success.
“We provided the best roof system possible for the job,” Worrell says. “The existing roof was about as teed-up as it gets for a fleece-back TPO membrane re-cover. We were able to identify and recognize re-covering with TPO membrane was the appropriate choice for all involved. The new membrane will provide the longevity and performance the building owner wanted. It reduced the time we had to be there and eliminated interruptions that would have come with a total tear-off, which was important to the hospital.”
Project name: University of Kansas Health System
Project location: Great Bend, Kan.
Project duration: July 2023- September 2024
Roofing contractor: Rhoden Roofing LLC, Wichita, Kan.
Roof system type: TPO fleece-back membrane
Roofing manufacturer: MuleHide, Beloit, Wis.
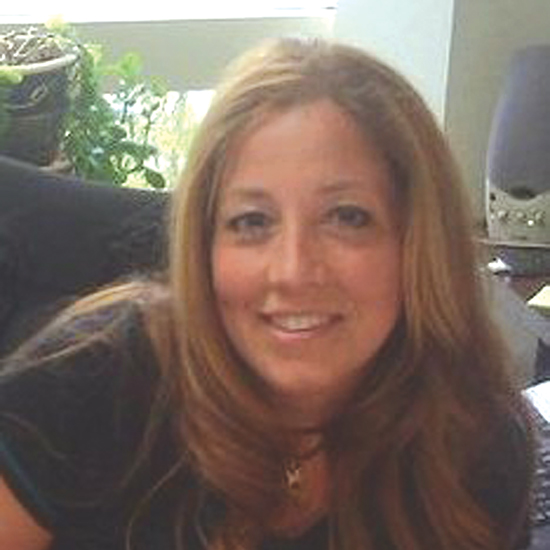
CHRYSTINE ELLE HANUS
Professional Roofing’s associate editor
Director of commmunications
NRCA